
Unlocking Efficiency: ASUS IoT Drives Smart Factory Development through AI

Introduction:
Industry 4.0 refers to the fourth industrial revolution characterized by the integration of advanced technologies, including IoT, AI, big data, and robotics, into manufacturing and industrial processes. It encompasses the digitization, automation, and interconnectivity of machines and systems, leading to increased productivity, efficiency, and innovation. In recent years, ASUS has actively invested in smart manufacturing by developing AIoT, or Artificial Intelligence of Things, a concept that combines artificial intelligence (AI) technologies with the Internet of Things (IoT) to create intelligent and connected systems. In 2018, ASUS created its sub-brand, ASUS IoT, with a specific emphasis on smart manufacturing, smart healthcare, and smart retail. Its primary objective is to deliver integrated hardware and software solutions, as well as customized AI and IoT offerings, to cater to the unique needs of customers in these domains. In 2021, ASUS built a brand new AI-powered demonstration factory to serve as the testing grounds for AIoT solutions. The factory can support the production of low-volume, high-diversity, and highly customized industrial computers to accelerate AIoT deployment.
Industry 4.0 promotes precise production and quick and flexible changes. It accelerates the progress of smart manufacturing in the manufacturing industry. How do we transform traditional factories into smart ones? To go from digitization to Industry 4.0, factories must move through six stages, computerization, connectivity, visibility, transparency, predictive capacity, and adaptability to develop smart brains and become smart factories.
Six stages in the journey to Industry 4.0
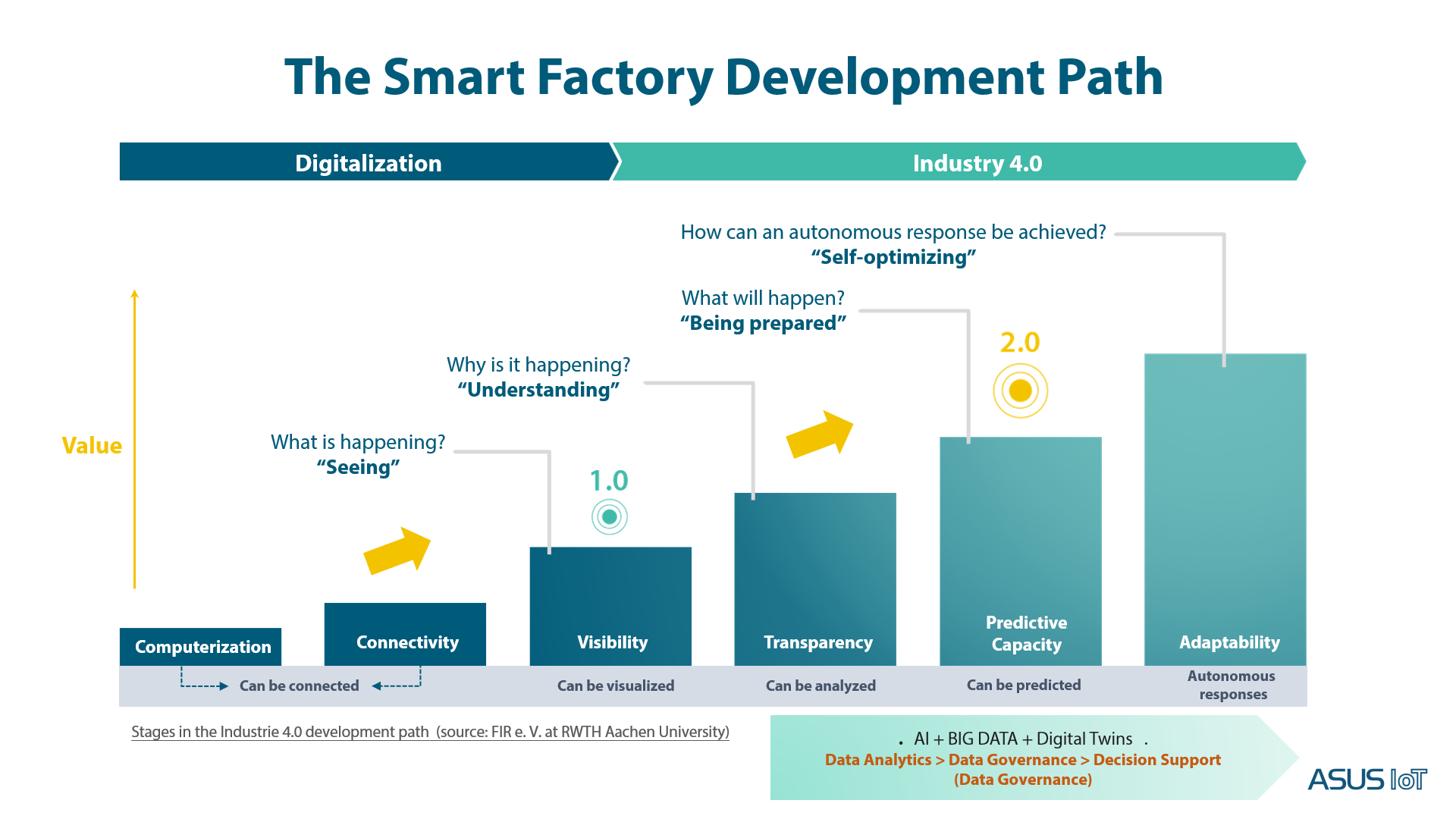
Figure 1: From digitization to intelligentization - smart factories will go through six stages
Digitization is the first step to making a factory smart, where computerization and connectivity are essential. Only by connecting equipment to the network and collecting production data through IoT, the factory's systems, and the manufacturing execution system (MES) can we fully understand the factory's equipment status.
Then, the factory enters the Industry 4.0 intelligentization process to visualize the data of the factory's equipment and make it transparent to help factory manager understand equipment operations and the causes of events. Predictive capacity is about using AI to analyze factory equipment data to generate insights and predict equipment health status and potential problems for preparations in advance. The last stage, adaptability, combines AI, big data, and digital twins to reach autonomous responses through data analytics, data governance, and decision support to realize the ultimate goal of self-optimization.
Two phases for building smart factories with AI
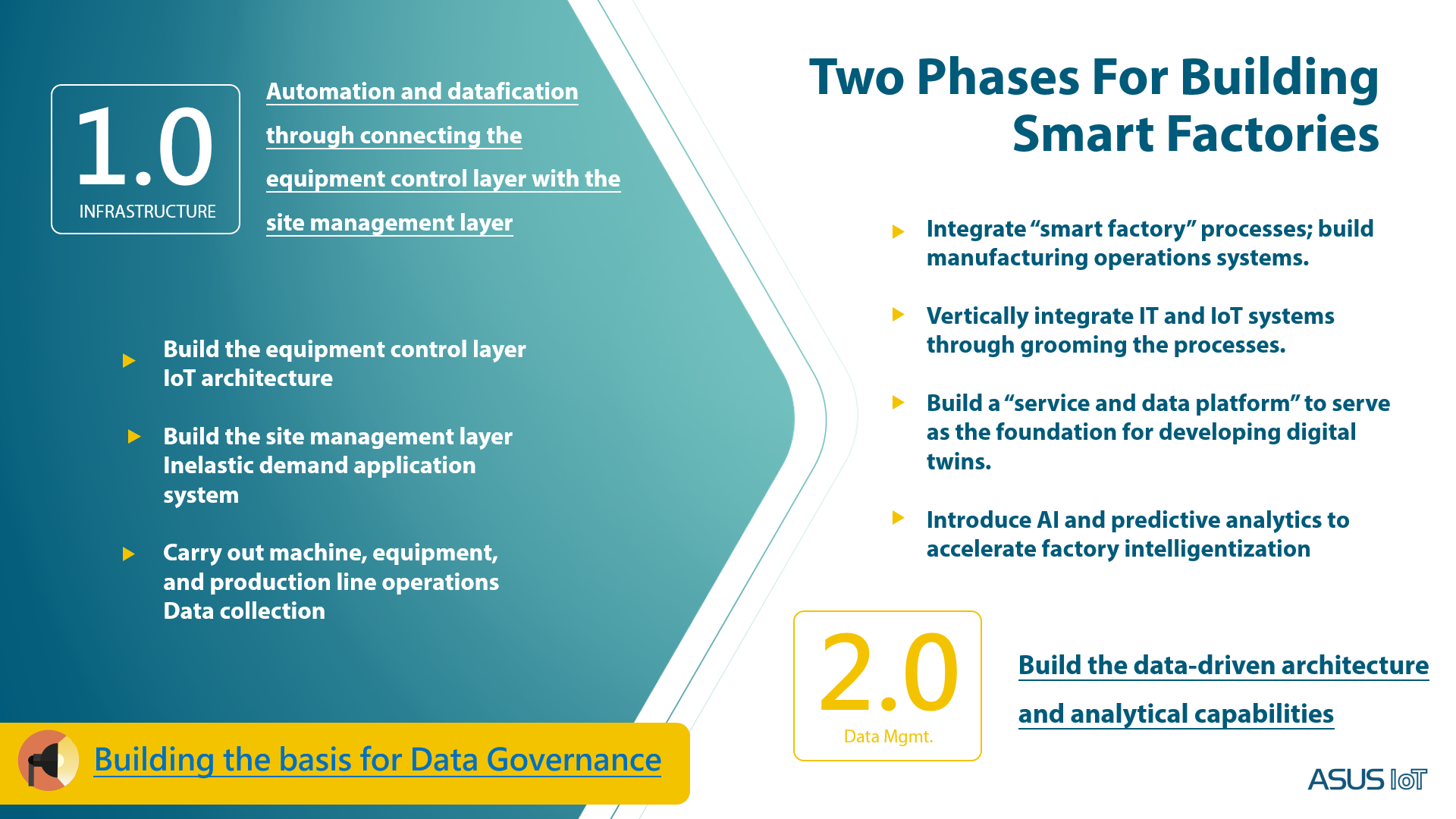
Figure 2: ASUS IoT develops smart factories in two phases to create data-driven analytical capabilities.
ASUS IoT divides the six stages of smart factories into two phases:
Phase 1 - Smart Factory 1.0: Realize automation and datafication through connecting the equipment control layer with the site management layer. Establish the smart infrastructure, deploy the equipment control layer through IoT and factory monitoring, and build the site management layer with the inelastic demand application system to operate equipment and production lines and collect data.
Phase 2 - Smart Factory 2.0: Focus on constructing data-driven architecture and analytical capabilities and introduce AI and predictive analytics to accelerate factory intelligentization. More specifically, vertically integrate IT and OT (operational technology) systems through grooming the processes, integrate smart factory processes, build a manufacturing operations management system, and create a service and data platform to serve as the foundation for developing a digital twin for the AI factory in the future.
Smart factory system architecture, a step towards next-generation factories
ASUS adhered to the core concept of pragmatism when establishing ASUS IoT. ASUS created the AI demonstration factory in Shulin District, New Taipei City, integrating IoT with M2M (machine to machine) and introducing AI solutions to launch comprehensive Industry 4.0 solutions. With the solutions, ASUS hopes to improve production quality, reduce costs, create smart, digital, and sustainable next-gen factories, and boost supply chain resilience to help the manufacturing industry transform faster with AIoT.
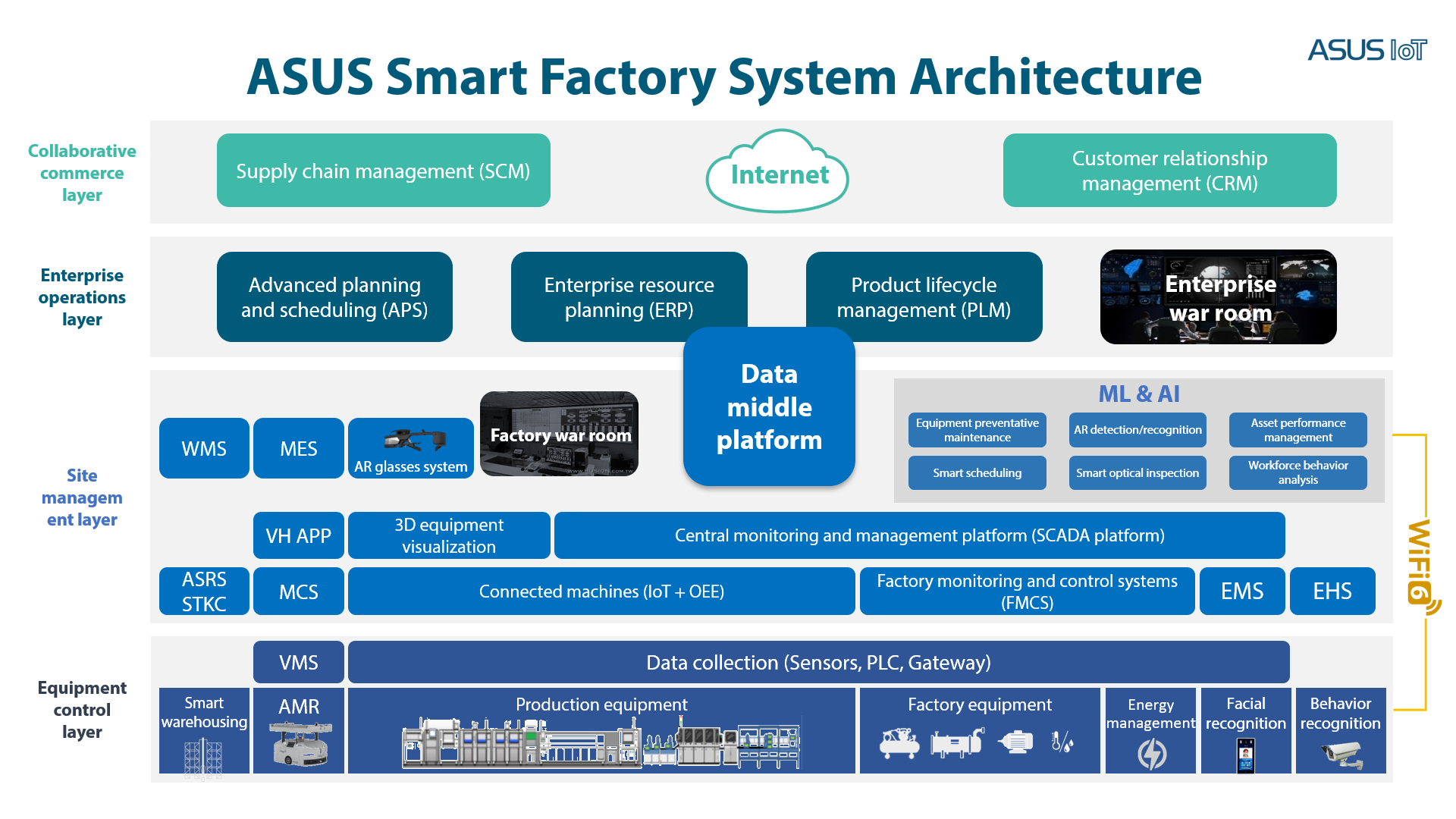
Figure 3: The key breakthrough of the smart factory system architecture designed by ASUS IoT is the connection between the equipment control layer, site control layer, and enterprise operations layer.
The smart factory system architecture designed by ASUS IoT for the new AI-powered demonstration factory divides AIoT into four layers, the equipment control layer, site management layer, enterprise operations layer, and collaborative commerce layer. The key breakthrough for collecting big data is the connection between the equipment control layer, site control layer, and enterprise operations layer. The following introduces the system architecture of the three layers:
1. Equipment control layer: Collects information related to production equipment, factory equipment, smart warehouses, face recognition access control systems, autonomous mobile robots (AMR), energy management, and gesture recognition through equipment sensors, PLCs (programmable logic controllers), and gateways.
2. Site management layer: Sends the information to the site management layer, including collecting production equipment data into the machine network, sending the factory equipment data to the factory monitoring system, and then sending the data from these two systems to the central monitoring and management platform via the network.
The site management system, AR glasses system, 3D equipment visualization system, AMR material handling system, and AI solutions developed with machine learning AI systems. The AI solutions include: AI defect detection before DIP wave soldering, AI defect detection equipment at the packaging stations, AR inspection and recognition, equipment preventive maintenance, and smart scheduling for reducing labor.
3. Enterprise operations layer: Opens up the site management layer and enterprise operations layer, connects IT and OT systems, builds the data and service management platform, and drives digital analytics capabilities to introduce AI predictive analytics to make the entire factory smart.
Integration and intelligentization, building a central monitoring and management platform
The motherboard production line of the AI demonstration factory includes five categories, SMT, DIP, assembly, testing, and packaging.
How do we understand the big data of an entire factory and make factory operations smart? Smart brains are indispensable. ASUS IoT and Shinewave together built an integrated and intelligent central monitoring and management platform that can comprehensively integrate the information of equipment in factories, site management, and enterprise operations, connect machines, MES systems, and factory monitoring systems to collect data in real time, including the utilization rate, quality indicators, labor indicators, production expenditure and costs, and labor safety protection monitoring, and provide 3D equipment visualization to visualize and present real-time data and data analysis results on the TV wall in the factory's war room to help factory managers make management decisions in real time, improve operational efficiency, and reduce production costs.
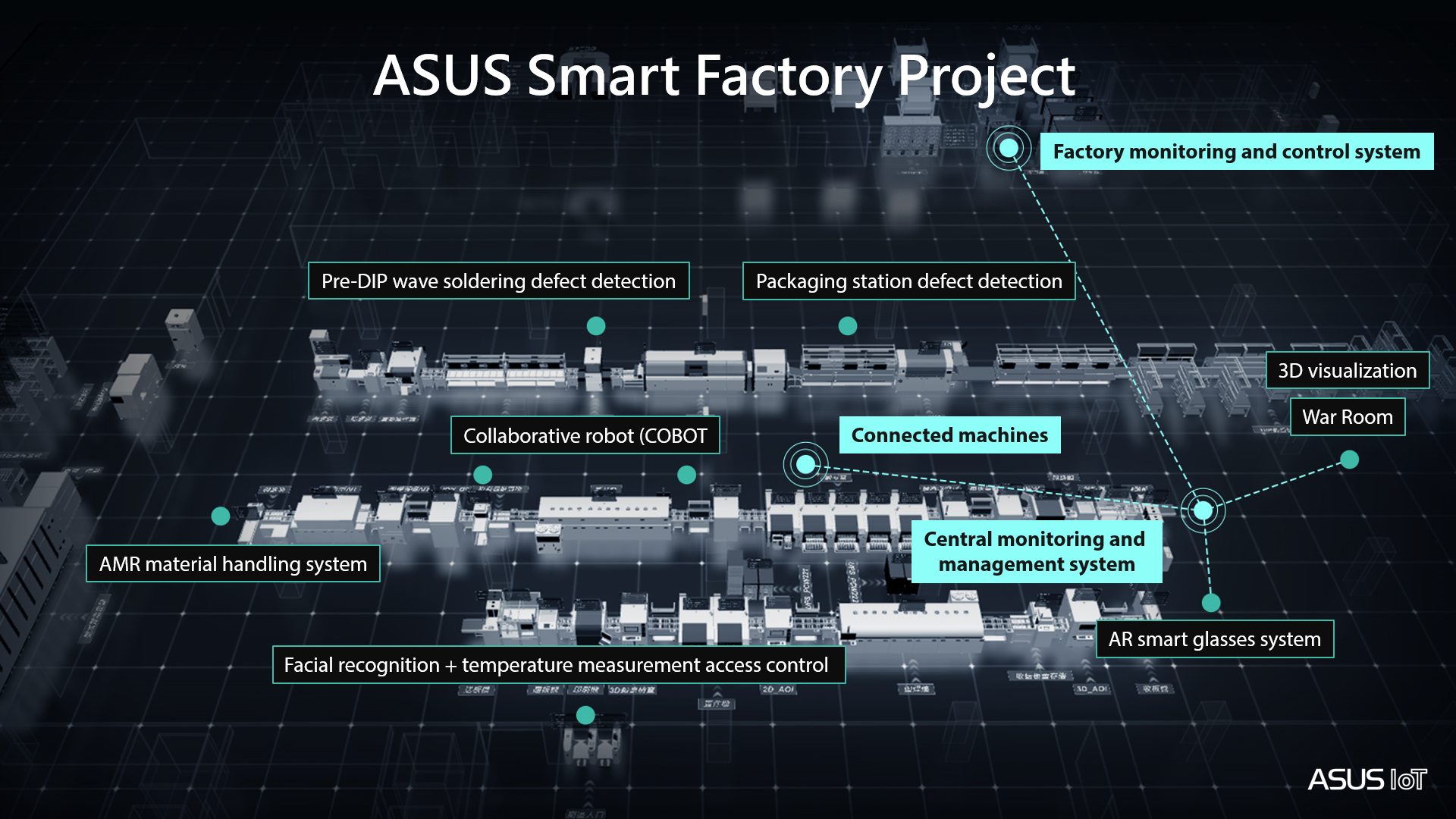
Figure 4: A 3D top view of the ASUS IoT AI demonstration factory in Shulin. The smart brain central monitoring and management system integrates the big data of the entire factory.
The AI-powered demonstration factory has become an experimental field for AIoT solutions, including pre-DIP wave soldering smart defect detection equipment, motherboard packaging defect detection equipment, AR smart glasses systems, face recognition access control systems, and AMR material handling control systems. The AIoT solutions first served ASUS Group's internal IoT industrial product manufacturing needs and are now expanding to partners, OEM companies, and external customers.
ASUS IoT developed the integrated software and hardware solutions for pre-DIP wave soldering smart defect detection equipment and motherboard packaging defect detection equipment in-house. To rapidly generate a new AI defect detection model, only a single photo of a defect-free product is required, utilizing AI as the detection engine. The process entails either automated selection based on CAD data or manual selection of the component to be inspected, enabling efficient creation of the model.The AI defect detection equipment adopts an intuitive human-machine interface, helping users to reduce the chance of operational errors. Moreover, the use of a line scan camera removes the size restriction of the motherboard to be detected and obtains the information on the production serial number of the product automatically. The detection results are highly precise. It can also be customized to connect to the MES system to record the status of the product during the production process, so that each product has a complete production history.
Pre-DIP wave soldering smart defect detection equipment reduces DIP production changeover time by 40%
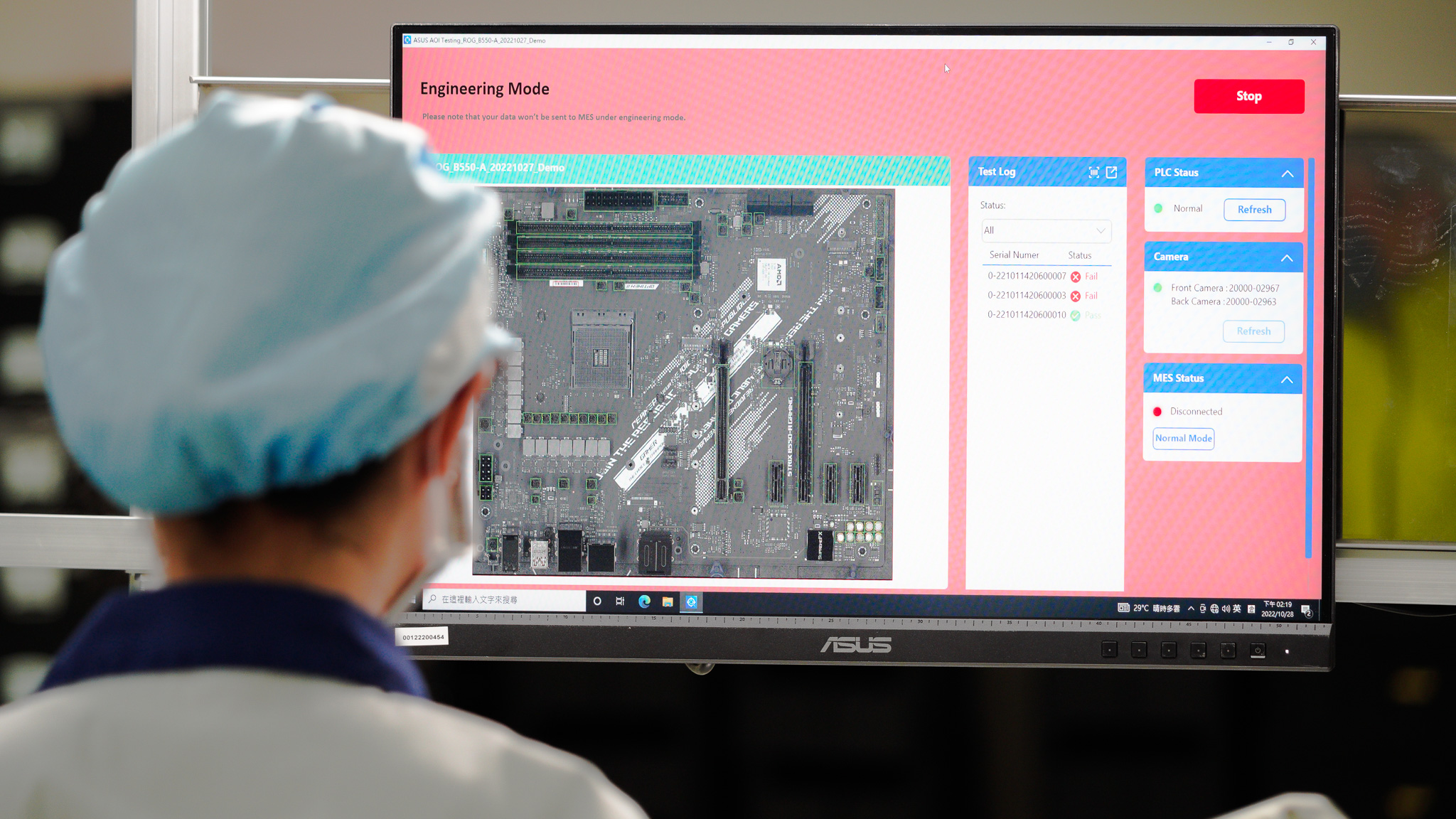
The manual plug-in process in the factory requires soldering electronic parts to motherboards with a wave soldering machine. In the past, factories had to establish an extra inspection line specifically for checking motherboards once they completed the wave soldering process. If a defect is detected, workers had to manually melt the solder on the plug-in and replace the part. The high temperature during this process damages the parts and the assembled circuit boards, gradually causing many production quality problems to emerge over time.
Second, factories used rule-based detection in the past. Engineers often had to program all the rules for catching defects on the motherboards throughout the night before production. Programming takes at least three to five hours and can last until dawn.
ASUS IoT introduced AI to develop the pre-DIP wave soldering smart defect detection equipment, which substantially changed the production process:
1. Prevent defect products from passing through the machine: Detection now takes place before soldering. AI defect detection comprehensively inspects plug-ins for defects, such as missing parts, wrong polarity, misalignment, and wrong parts. The errors spotted by AI are marked by a red box on the screen so that workers can fix the errors before the parts are soldered onto the motherboards. Doing so reduces the scrap rate by 14%.
2. Make rework less complicated: The number of post-machine workers needed is reduced from 3-5 to 1-2.
3. Shorten the preparation period: The hours of preparation in the past is reduced to 15 to 20 minutes, reducing the overall DIP production line set-up time by 40%.
Smart defect detection equipment at packaging stations increases PCBA first pass yield rate by 20%
Before a motherboard is packaged into a colored box, the CPU socket pins and the PCBA will be tested and inspected at the final packaging station.
In the past, workers had to evaluate whether the pins were correctly aligned or broken. Workers may also forget to switch the control position of the pins to the ship state. However, it was impossible to manually record the defects one by one during the inspection process. Also, there are many CPU socket pins, and they are thin. Thus, bending the pins or letting foreign matters enter when trying to fix a defect is easy. Thus, if consumers receive defective products, it is difficult to confirm which step in the production process is the cause.
The packaging station smart defect detection equipment developed by ASUS IoT can automatically detect motherboard defects to prevent defective products from being packaged and placed on the market. The introduction of AI defect detection equipment has reduced the amount of human resources required at the maintenance station by 50%, and increased the PCBA first pass yield rate by 20%. The detailed product production history has also boosted the consumer experience.
Smart defect detection equipment at packaging stations increases PCBA first pass yield rate by 20%
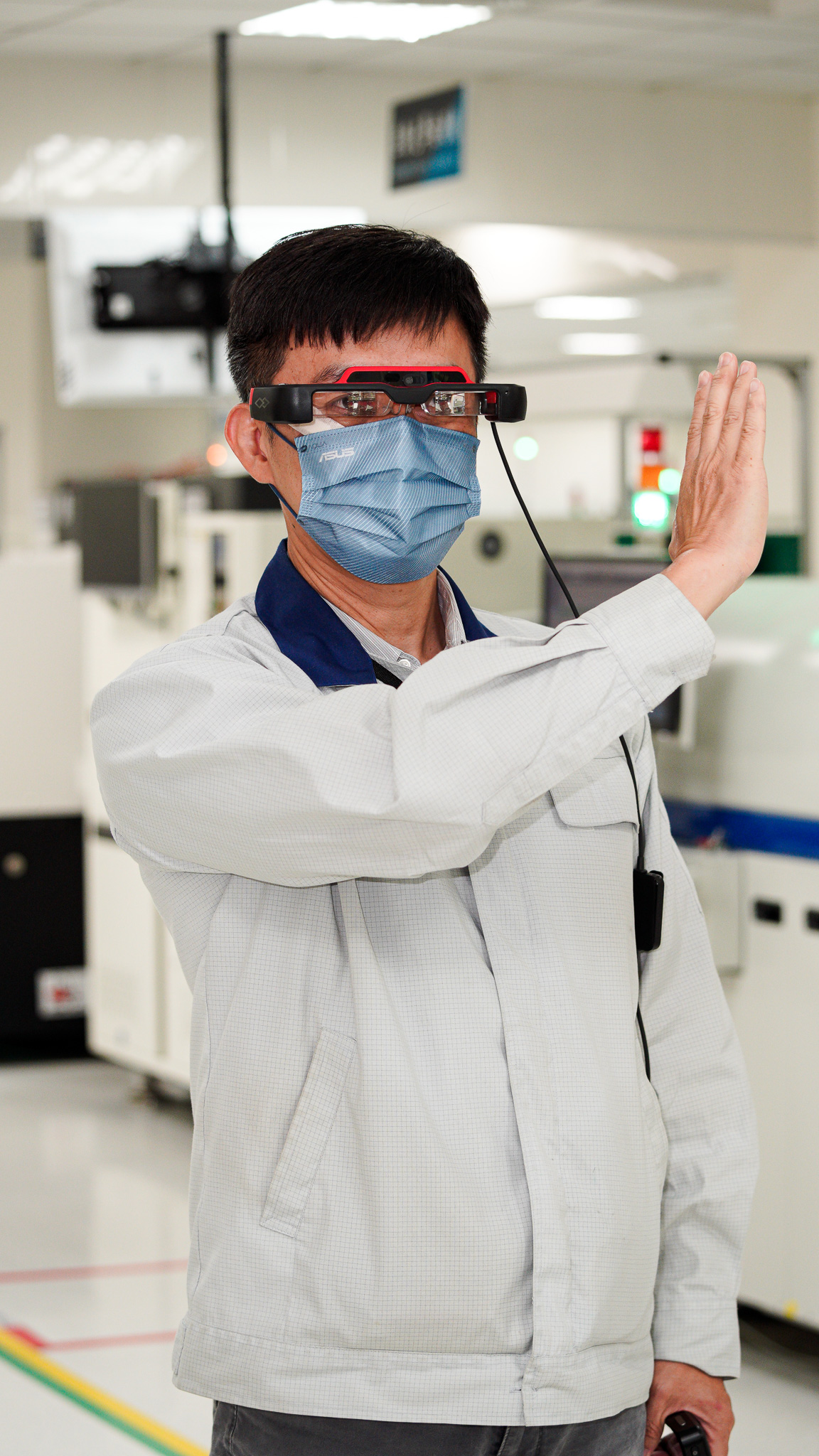
ASUS IoT has also introduced an AR smart glasses system into the AI demonstration factory's production, presenting a smart production process that integrates virtual reality and helps factory workers understand production process information in real time.
There are currently three usage scenarios for AR smart glasses: remote collaboration, smart mobile war room patrol, and real-time information on the mobile war room's displays. The scenarios are described below:
1. Remote collaboration: AR smart glasses allowed factory equipment to continue to operate during the pandemic. When equipment problems occur, a factory worker can put on AR smart glasses and turn on the camera. The AR smart glasses will overlay the image onto the scene so that remote equipment experts can work in sync with the factory worker. They can understand the site and equipment status from the AR smart glasses perspective and collaborate remotely to complete repair, inspection, maintenance, and training operations.
2. Smart patrol: In the past, workers had to carry laptops to inspect equipment and check equipment specifications or parameter records. Now, workers can work hands-free. All they need to do is scan a machine's QR code with AR smart glasses, and the central monitoring and management system will project the real-time data produced by the equipment to the glasses so that workers can repair equipment directly. This new method improves machine patrol by improving inspection efficiency, ensuring production line machinery operate steadily.
3. Real-time information displayed at the beginning of a production line: A visual display can be placed at the beginning of each production line in the factory. In the past, workers had to walk to the end of a production line to see the information. The advantage of AR smart glasses is that the workers can scan QR codes anytime, anywhere, and the information of the production displays will be projected onto the glasses. Workers can understand the production status and production line indicators in real time, without running back and forth to check the display at the end of the line, therefore saving time.
AR smart glasses are connected with the central monitoring and management platform, giving the factory a mobile war room and making factory management more convenient as workers can keep abreast of production information of the production lines and the current capacity of equipment, facilitating real-time decision-making.
In the future, ASUS IoT hopes to utilize AR smart glasses for confirming the incoming, retrieving, loading, and connecting process of materials, assembly, and shipping.
AMR material handling control systems boost material handling efficiency
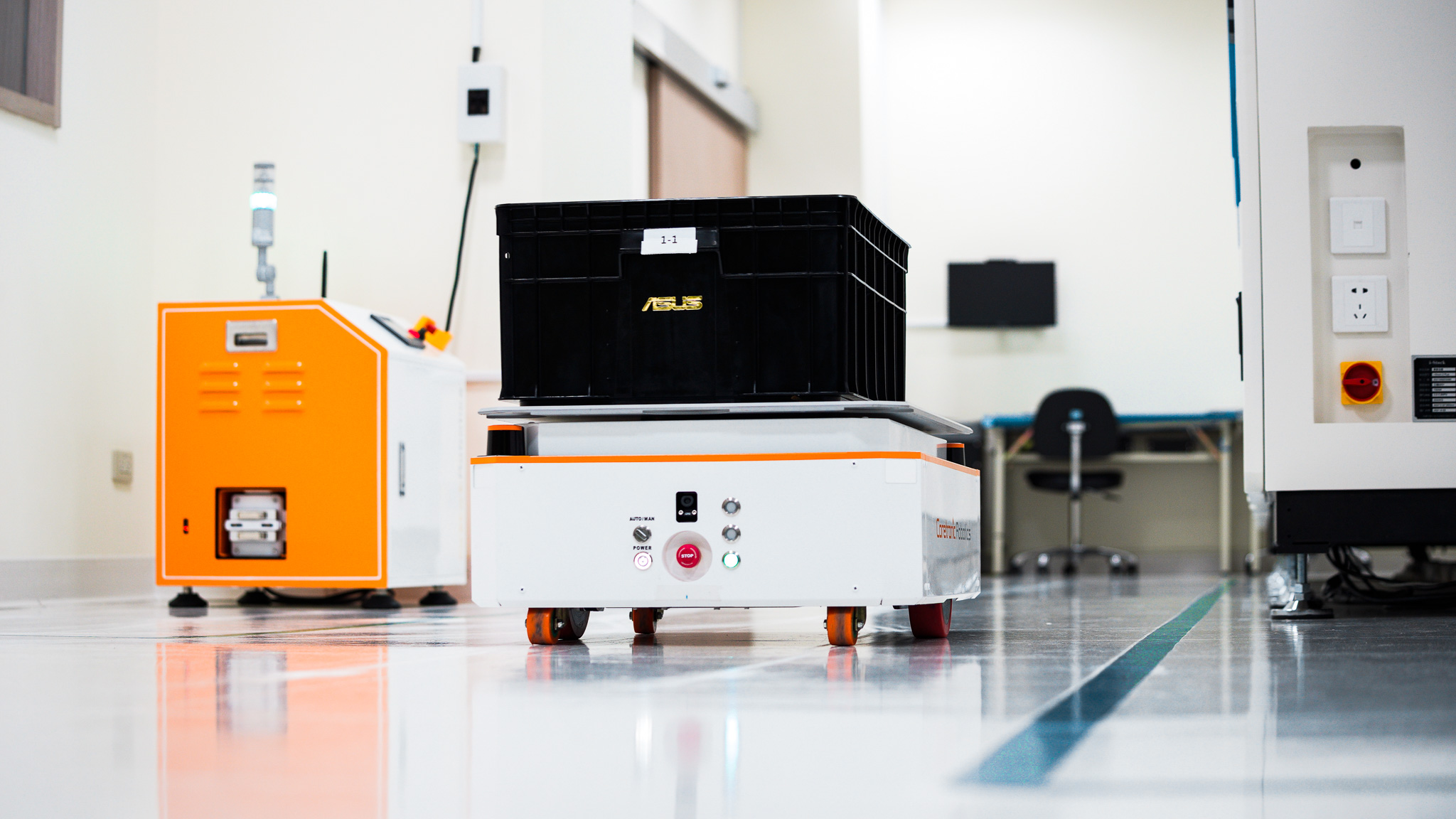
How do we boost material handling efficiency for smart factories' low-volume and high-mix and frequent changeover production models? ASUS IoT developed AMR and material handling control systems that integrate MES systems and smart warehousing intelligently. When the MES system sends out work orders, the smart warehousing system will automatically prepare the materials and notify AMRs to transport them to automate the process.
This system allows workers to control material handling tasks in real time, reduces the rate of manual handling errors, improves material transport efficiency, and saves workers time from transporting materials back and forth between the smart warehousing system and the materials preparation area of the SMT production line. The human resources required for handling is reduced by half, and the time it takes to retrieve materials and reels is reduced by 50%. It also increases the productivity of the SMT production line by 20% and reduces the changeover time by 54%.
Currently, ASUS IoT has completed Smart Factory 1.0. In the future, ASUS IoT hopes to build a data-driven architecture and analytical capabilities and integrate digital twins with various AI solutions to achieve the smart factory goal and make factories smarter.
The ASUS Group combines decades of internal experience and resources in the consumer electronics industry, gathers industrial computer-related subsidiaries, and forms external alliances with rich upstream and downstream companies. ASUS IoT will utilize the group's distribution, procurement, and manufacturing advantages to promote AI transformation and digital resilience to move the industry toward the Industry 4.0 transformation goal.